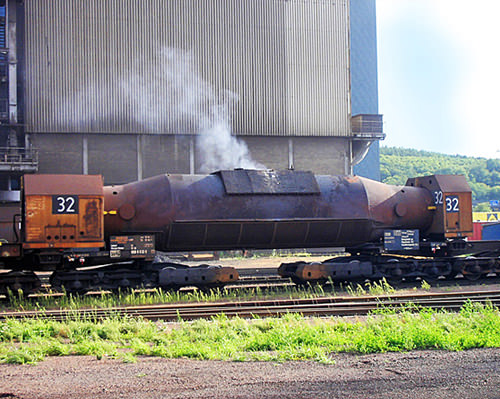
A torpedo ladle is used to transport molten iron from the ironmaking section of the plant to the steelmaking section. Under normal conditions, the residence time of the molten steel in the ladle is 2 to 4 hours, and the distance traveled is usually less than half a mile. In addition to transporting molten iron, torpedo can also be used as a refining container. For example, in the desulfurization process, the powdered reagent is injected into the molten iron through a spray gun. The reagent reacts with the sulfur in the molten iron and separates from the iron in the form of slag. This process is detrimental to the refractory lining due to turbulence.
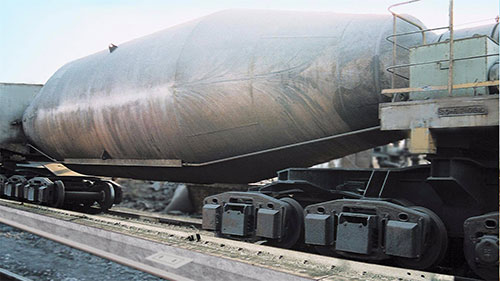
Lite recommends partitioning the refractory lining in the slag line to minimize any refractory damage that may occur during this operation. Lite also offers two different lining designs for torpedo lathes: maintenance-free linings that do not require regular jet maintenance and traditional high-aluminum linings designed to be maintained with spray supplies.
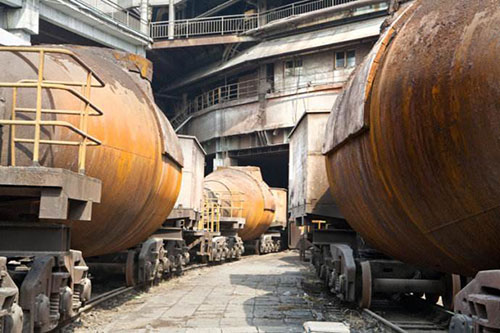
Lite's maintenance-free lining is designed to run the entire torpedo ladle movement on the original refractory lining without the need for shotcrete maintenance. Therefore, the process of initial refractory-mounted bricks is critical - all joint sizes must have a minimum thickness. This refractory-designed ladle is capable of transporting 400,000 net tons of molten iron without any maintenance. The key to the maintenance-free lining design of Lite is the 80 aluminum content SiC brick and carbon bonded, alumina SiC brick product.
Conventional torpedo ladle refractory designs include high alumina bricks (70 high alumina bricks) and alumina/silicon carbide/carbon (carbon bonded, alumina silicon carbide brick products) impact mats. These linings are designed to be sprayed with concrete (high alumina spray) and/or intermittent spray feed.