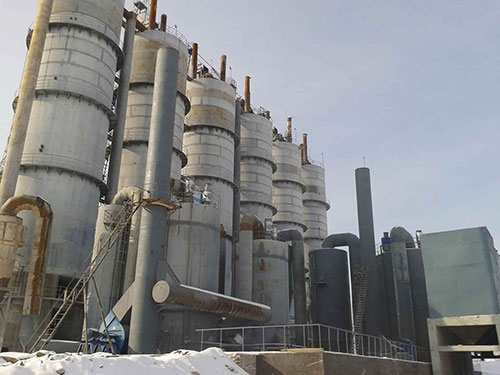
The lime recovery kiln is a long rotating cylinder set on a slight slope and the lime mud is fed into the uphill feed end. The rotation of the kiln together with gravity causes the lime mud to face downward toward the burner at the lower end of the kiln. The final product leaving the lime recovery kiln is calcium oxide, which undergoes many other chemical treatments before being used to regenerate the white slurry.
The lime recovery kiln can be up to 380 feet long and up to 15 feet in diameter. These vessels are refractory lining and are generally divided into five main sections, including the section, the drum section, the intermediate section, the combustion zone and the refractory dam. The operating environment of each part is different and determines the choice of refractory material.
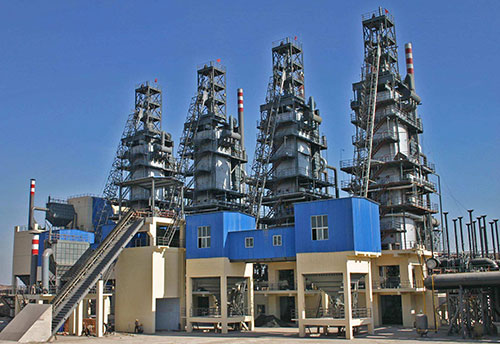
Chain part:
The segments are designed to function as heat exchange devices by increasing the surface area of the lime mud exposed to the hot gases. The operating temperature of the segments is relatively low. The integral refractory material is typically used in the chain portion of the lime recovery kiln and must be able to withstand the significant impact and wear of the chain and incoming lime mud. High alumina cement, coarse aggregate castables, low cement castables, exhibit consistently good results.
Rotary section:
A tumbler, also known as a lifter, is also designed for use as a heat exchange device. The inverted cup is a raised portion of the refractory material that is raised and mixed as the lime feed is run in the direction of the kiln. This mixing process helps to ensure that the lime feed sees a more uniform heat distribution during the calcination process. The refractory brake cup is usually a prefabricated overall shape. Lite's low cement castables have a proven track record in prefabricated refractory glass and utilize Lite's proprietary fastening system to provide a secure fixed kiln shell.
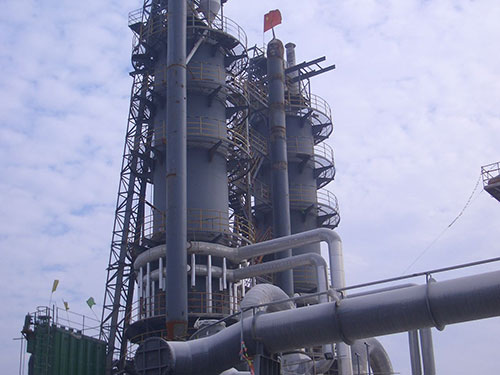
Middle area:
As the lime feed enters the intermediate zone, the operating temperature becomes milder. Historically, refractory clay, 50% alumina and 60% alumina refractory bricks have been used in the intermediate zone. Lite's clay bricks, 50 high aluminum bricks and 60 high aluminum bricks have proven to be a successful history of service in the middle ground. Lite's insulation bricks are high-strength insulating refractory bricks that provide a reliable service life to support insulators while reducing heat loss. Insulation bricks are about half the density of high alumina bricks, but are still strong enough to support the mechanical stress introduced by the rotary motion of the kiln.
Burning area:
The refractory material in the combustion zone of the lime recovery kiln is affected by the highest temperature and is most susceptible to chemical attack. The temperature in the combustion zone can be as high as 2500 °F. Lite has chosen 70% alumina bricks for many years.
Lite also offers 75 high aluminum bricks. Another option for these mills for abrasive wear that has experienced refractory lining due to alkaline attack at elevated temperatures is magnesium spinel brick.
Refractory dam:
Refractory retention dams have become more common in modern lime recovery kilns. The dam increases the retention time of the feed and makes the calcination process more efficient. The material is made of Lite's 60 aluminum low cement castable, etc.