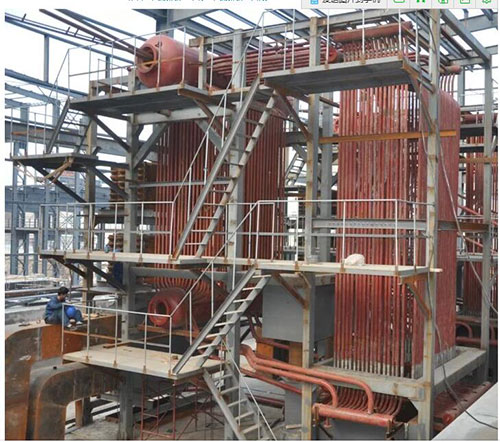
Circulating fluidized bed boilers operate at temperatures that are not conducive to nox emissions, and 95% of SOx emissions can be controlled by increasing fuel flow.This, combined with the value of being able to constantly acquire and convert to the lowest cost fuel flow, makes the equipment more economical to operate.
The process involves injecting forced air under the fuel bed.During the combustion process, a strong air flow is generated, bringing the combustion products and unburned fuel into the equipment's piping.The cyclone is used to separate the combustion product from the heavier unburned fuel and send it back to bed.This process leads to high fuel conversion rates and reduces the waste stream in the process to air powder.
The refractories in circulating fluidized bed boilers can have very different refractory requirements.Lite company refractory is known for its abrasive nature of the process and is designed to resist abrasion, impact and high temperatures.
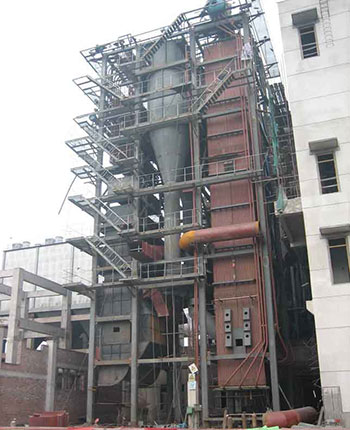
Lite has a long history of providing refractory materials for circulating fluidized bed boilers.We know that these highly abrasive environments require some wear-resistant solutions, such as sprayers and 60 mullite bricks, and silicon carbide sprayers.Lite can not only provide solutions like this, but also for any other part of the circulating fluidized bed boiler equipment.