Blast furnace technology has been the main method of producing iron for decades. A blast furnace is a round shaft with a refractory lining that is 100 to 200 feet high and has an inner diameter of 20 to 45 feet. The wall lining is usually 2 feet or more thick and contains over 2,500 tons of refractory material. Blast furnaces produce iron by exposing iron ore, iron particles and sinter to high temperatures and carbon monoxide (a reducing agent). Coke is the main fuel.
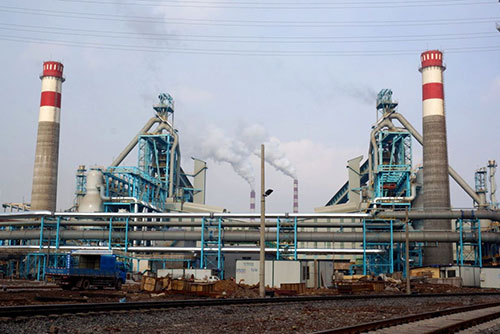
The preheated air from the hot blast furnace is also injected into the furnace through the tuyere. The tuyere surrounds the furnace at the top of the furnace, where incomplete coke combustion occurs. Burning releases a considerable amount of heat and creates very hot carbon monoxide reduction gases, reducing the amount of gas swept upward through the ingredients. Iron oxide reduction begins when the ore is in contact with the reduced gas, and it is usually carried out in stages to form metal iron with high carbon content. Iron gathers in the furnace to form a molten pool. Since there is no opportunity to repair refractories during operation, the length of blast furnace activity time mainly depends on the service life of refractories.
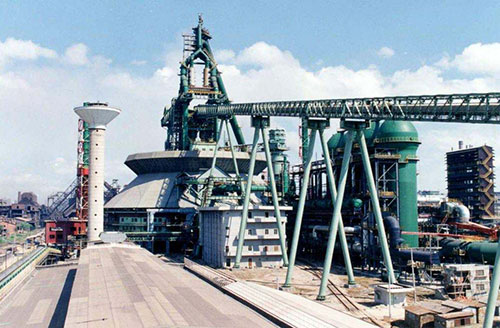
Lite offers complete refractory packages that are proven to maximize the service life of the furnaces. From the bottom of the furnace through the hearth and chimney, the refractory design will vary due to the conditions of use and destructive forces in each area of the furnace. Lite will work closely with you to ensure that all requirements are met, and choose the appropriate material (75% high alumina brick, 65% high alumina brick ® or high strength refractory brick) used in each part of the furnace. Several alternatives are available, depending on the cooling design and activity objectives of the furnace.
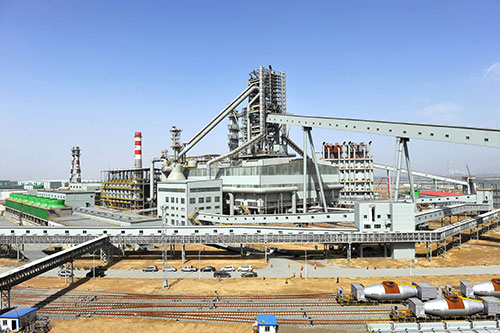