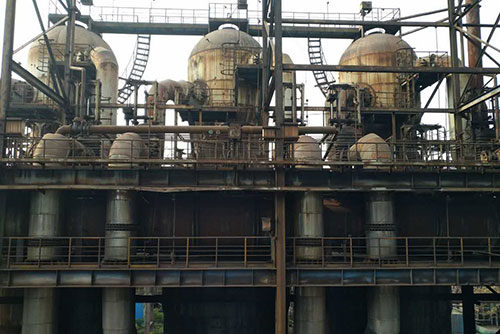
Blast furnace operation requires a lot of preheating air. The temperature of preheat air of hot blast furnace must be 2000 ° F to 2400 ° F. The air is transported to blast furnace vents through a series of large refractory lining pipes called hot air ducts and hot air coils.
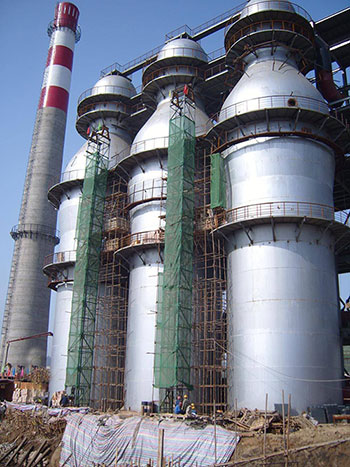
Each blast furnace usually consists of three or four stoves which, in turn, serve the furnace. That is, one or two stoves provide the hot air to the furnace, while the remaining stoves provide "fuel gas". When gas is burned, the combustion takes place in the combustion chamber of the furnace, and the hot gas is discharged through the lattice brick, heating the lattice brick in the process. When "explodes," the cycle reverses. A blast of cold air entered the furnace from under the inspector. It is heated as it passes through the hot inspector and leaves the furnace through the hot air outlet to the hot air main.
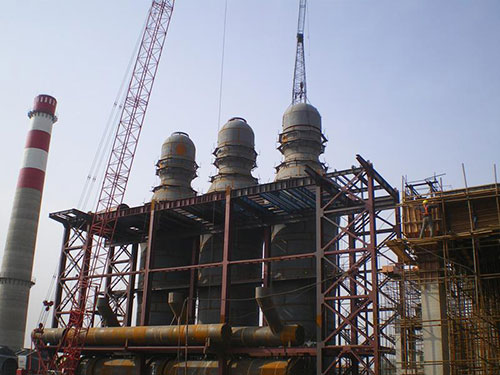
During the operation of the furnace, the temperature in the upper part of the combustion chamber, the dome and the upper part of the lattice brick can range from 2200 °F to 2600 °F. The temperature below the lattice brick is as low as 600 °F.
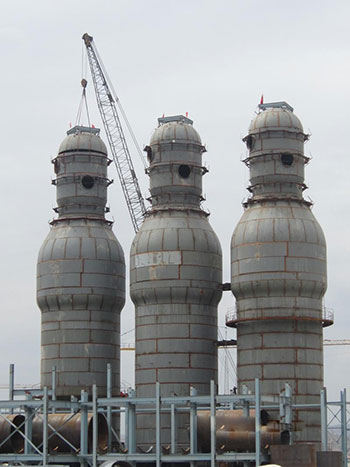
The partition of refractories is used to minimize the cost of refractories. Lite recommends: 60 andalusite high alumina brick is used in the highest temperature part and the middle temperature part of the furnace. 50 high alumina bricks are used for lower temperature parts. Since there are many product subdivisions in a hot blast furnace, the design and operating parameters of the given furnace must be specified to ensure that the most economical refractory products can be installed in each area.