A tunnel kiln is a special kiln structure for the production of homogeneously sintered ceramics, bricks and other refractory materials at high temperatures.
Tunnel kilns usually consist of a series of connected bricks, refractory bricks or prefabricated panels arranged along a horizontal track. The interior of the kiln is divided into different zones, including preheating, sintering and cooling.
During production, ceramics, bricks or other refractory materials are placed on kiln cars or on an assembly line and then continuously conveyed through a tunnel kiln. Fuel is burned in the kiln to provide heat, and the heat is conducted and radiated to the product through the kiln wall, making it gradually warm up.
As the products pass through the preheating zone, they gradually heat up to the temperature required for combustion before entering the sintering zone, which is a critical zone for achieving the desired physical and chemical properties. In the sintering zone, the product undergoes high temperature treatment, undergoes thermochemical reactions, and develops a dense structure and desirable physical properties.
After sintering, the product enters the cooling zone, where it is cooled by air to stabilize the temperature and structure. Finally, after the kiln car exits the kiln, the product is packed and stored.
Due to its continuous operation and high efficiency, tunnel kilns are widely used in industries such as ceramics, bricks, building materials and refractory materials. It enables mass production, saves energy and labor costs, and ensures product consistency and quality.
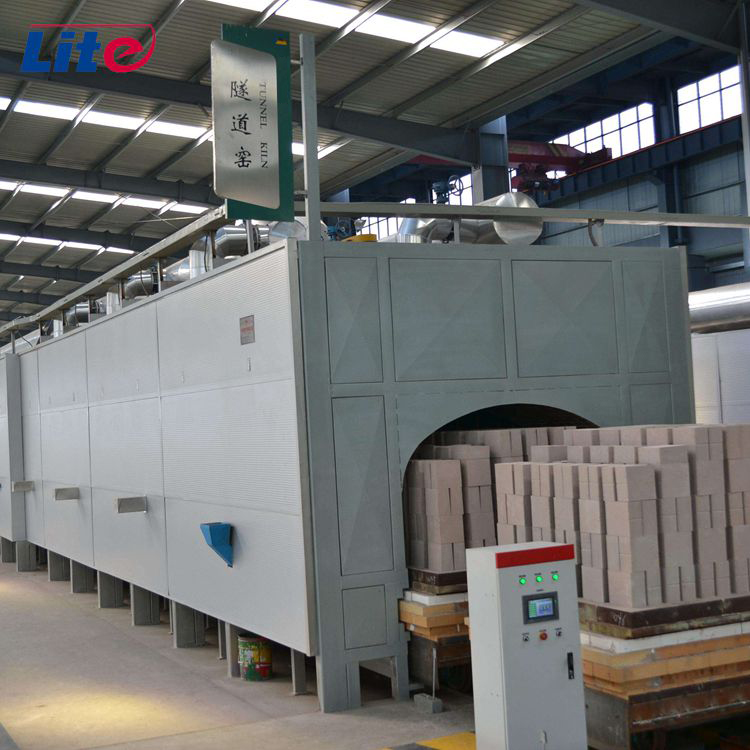
Tunnel kilns usually consist of a series of connected bricks, refractory bricks or prefabricated panels arranged along a horizontal track. The interior of the kiln is divided into different zones, including preheating, sintering and cooling.
During production, ceramics, bricks or other refractory materials are placed on kiln cars or on an assembly line and then continuously conveyed through a tunnel kiln. Fuel is burned in the kiln to provide heat, and the heat is conducted and radiated to the product through the kiln wall, making it gradually warm up.
As the products pass through the preheating zone, they gradually heat up to the temperature required for combustion before entering the sintering zone, which is a critical zone for achieving the desired physical and chemical properties. In the sintering zone, the product undergoes high temperature treatment, undergoes thermochemical reactions, and develops a dense structure and desirable physical properties.
After sintering, the product enters the cooling zone, where it is cooled by air to stabilize the temperature and structure. Finally, after the kiln car exits the kiln, the product is packed and stored.
Due to its continuous operation and high efficiency, tunnel kilns are widely used in industries such as ceramics, bricks, building materials and refractory materials. It enables mass production, saves energy and labor costs, and ensures product consistency and quality.
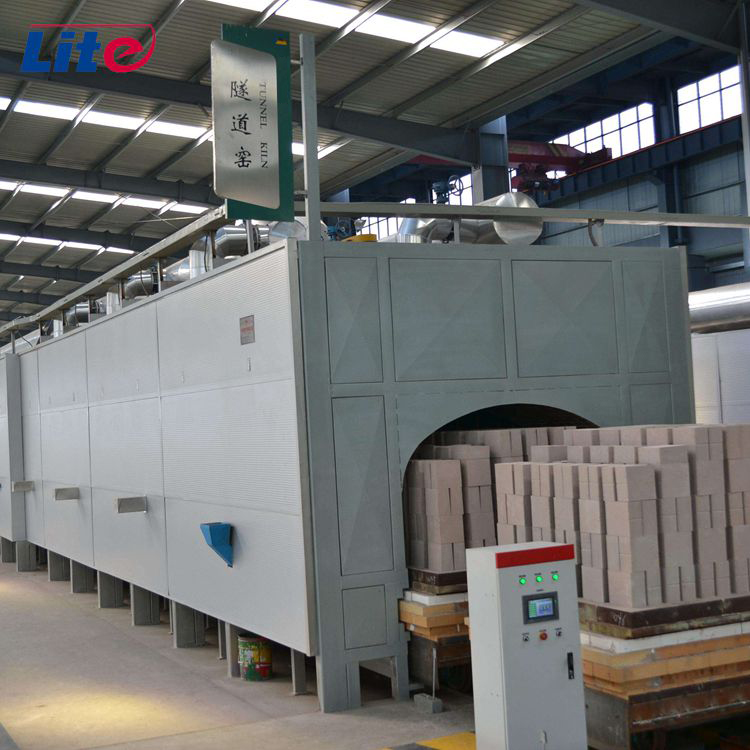